Editor’s Pick: Personal 3D Printer Uses Engineering-Grade Materials

The AW3D HDx 3D printer from Airwolf 3D can use high-temperature materials such as polycarbonate, bridge nylon and nylon 645 to fabricate prototypes. Image courtesy of Airwolf 3D.
May 28, 2014
Dear Desktop Engineering Reader:
It’s difficult to imagine that a personal computer was once something you showed off to visitors with false modesty. After all, I paid 1500 smackers for a dual floppy drive, 64K monster in the early ‘80s. That would be over 3300 greenbacks today, so you bet I paraded people by my gleaming wonder. Still, the best thing about affordable personal computers was that they unleashed creativity. Gazillions of people suddenly had a way to quickly and easily compose their thoughts, learn to program, design church newsletters and what have you. In some ways, today’s Pick of the Week is as much about unleashing your creativity — both at home and at work — as it is about the product.
The product is the AW3D HDx 3D printer from an outfit called Airwolf 3D in Costa Mesa, CA. This printer builds off and upgrades the base technology deployed in some of the company’s earlier generations of 3D printers and couples these enhancements with some new technology. Keep that last point in mind.
The short of it is that the AW3D HDx 3D printer is a desktop-sized prototyping system (24 x 18 x 18 in.; 39+ lbs.). It offers a 12 x 8 x 12 in. build envelope, and resolution can be as fine as 0.002-in. Based on the photos and videos, you might find that its tempered glass enclosure reminds you of those tower cases Tiger Direct sells to DIYers building their own PC with running lights. You can see the colored filaments winding around to the print nozzle, the prototype under development and lots of the unit’s internal organs.
The AW3D HDx 3D printer has two key attributes. The first is that it’s affordable — a hair less than 3500 bucks. And that brings up the AW3D HDx’s second noteworthy attribute.
This personal 3D printer can build your prototypes out of engineering-grade materials such as polycarbonate, bridge nylon and nylon 645. It can handle a lot of your traditional lower-temperature thermoplastics as well and without making you fuss around switching nozzles. You just change the filament.
Still, engineering-grade materials out of a desktop 3D printer suitable for both home and work environments? Really? Those materials require sustained high temperatures, which means they usually are the province of much more expensive systems.
The trick here is that new technology mentioned above. The AW3D HDx uses the company’s JRx hot end for 3D printers. Basically, the JRx can continuously hold temperatures of up to 599 °F (315 °C), which lets you use those more durable materials. Airwolf says the JRx incorporates some patent-pending technology that integrates Teflon to feed materials through the hot end and thus extrude a layer of materials. A proprietary thermal barrier between the Teflon and heater ensures everything runs smoothly.
The potential here seems boundless. Well, OK, maybe it’s not practical to make a life-sized model of Godzilla. But engineering and design offices could conceivably afford multiple AW3D HDx 3D printers. And, depending upon your application, the ability to use engineering-grade materials means that you can get into creating some small-run and even one-off production parts, which could be a new line of business for small design and engineering firms. For the entrepreneur working out back in the garage, this could be as liberating as the first personal computers for the home were. Not to mention that this could be a cool thing you can show off to the in-laws visiting from Peoria.
You can learn more about the AW3D HDx 3D printer by hitting today’s Pick of the Week link. The printer is so new that there is only a promised video on it on the landing page, but you can click the links at the end of the main write-up to watch a video on the AW3D HDx’s older sister, the HD (no ex), and the JRx hot end. Good stuff.
Thanks, Pal. — Lockwood
Anthony J. Lockwood
Editor at Large, Desktop Engineering
Read today’s pick of the week write-up.
This is sponsored content. Click here to see how it works.
Subscribe to our FREE magazine,
FREE email newsletters or both!About the Author

Anthony J. Lockwood is Digital Engineering’s founding editor. He is now retired. Contact him via de-editors@digitaleng.news.
Follow DE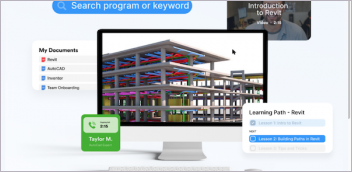
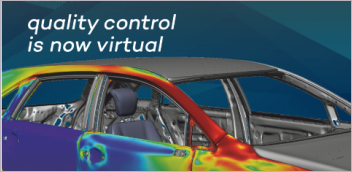
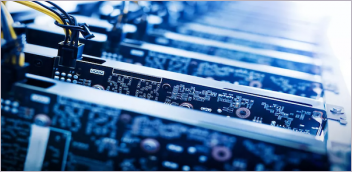
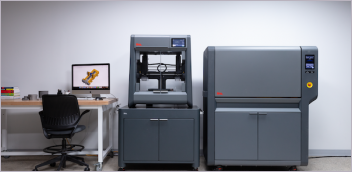