EDEM Updates its Flagship Software
Features and tools are being introduced, including a Python library for easier post-processing of large amounts of data, the ability to simulate deformable geometries as well as a new breakage model.

Mixer simulation including 10 million particles. This type of simulation can benefit from adding GPUs in parallel. Image courtesy of EDEM.
Latest News
December 14, 2018
EDEM announced the release of the latest version of its flagship software. Features and tools are being introduced, including a Python library for easier post-processing of large amounts of data, the ability to simulate deformable geometries as well as a new breakage model.
Here are the highlights of this release:
EDEM Multi-GPU Solver
EDEM 2019 officially introduces the EDEM multi-GPU solver engine. Using multiple GPU processors increases the maximum size of simulation that can be run on GPU as well as increasing performance. This means users can run large simulations faster but it also opens more possibilities to run much larger simulations that would not be possible on CPU only.
Performance gains from adding a second GPU range between 30% and 90% depending on the distribution and size of the simulation.
The multi-GPU solver has been developed on OpenCL thus providing flexibility for users to use either AMD or NVIDIA cards.
EDEM API on GPU
A key advantage of EDEM is EDEM API (Application Programming Interface), which enables users to write custom physics to model complex and advanced material behavior such as flexible fibers, sticky solids and breakage, the company reports. With EDEM 2019, API models can now be run directly on the GPU solver.
Being able to simulate how a geometry is being deformed as a result of a bulk material acting on it is something that is of key interest for numerous applications and which has been under development at EDEM.
The EDEM solver engines have been enhanced to facilitate continuous modification of a geometry structure during simulation. This means geometry sections can change shape and deform with input via the EDEM Coupling Interface. This enables users to directly couple EDEM to flexible body simulations to cover a wide range of applications such as belts, sheet panels, elastic membranes and more.
Processing Data with ‘EDEMpy’ Tool
The ability to run larger simulations means that there is a high volume of data that is generated. EDEM has developed a tool called ‘EDEMpy’ that can be used to process this large amount of data. EDEMpy is a Python library for post-processing and analysis of EDEM simulation data and takes advantage of the EDEM .h5 file structure. Using the library, users can extract specific data from a simulation deck and process that data in a customizable and reusable way. Users can, for example, extract force acting on a specific geometry over time and compare results back to back between multiple simulation decks, track particles residence time over the course of a simulation, visualize networks of contacts and bonds in a new flexible way, visualize DEM data as a continuum or use EDEM data to calculate post-processing properties for their simulations such as segregation index or tortuosity.
In this example users wanted to calculate a parameter called segregation index to quantify the extent of mixing as a function of time. Calculating segregation index for this 10 million particle mixer over 10 seconds required calculations to be made on 4.8 billion contact pairs. This was achieved by using EDEMpy
New Breakage Model
EDEM is releasing a beta version of a new breakage model that is able to describe fracture of particles subjected to repeated loading by simulating both surface degradation and body breakage. This advanced model considers both catastrophic breakage (due to high impact) as well as surface breakage (due to abrasion).
To develop this breakage model EDEM followed the latest advances in research and worked with experts in the field to deliver a robust model based on well-established and validated physics. The breakage model is able to provide key outputs related with the weakening of the particles and their related energies before and after breakage, as well as the final fragmentation and the size distribution of the fragments. This is the first breakage model able to address the different mechanisms of breakage including both surface damage and fragmentation.
Sources: Press materials received from the company.
More Info
More EDEM Coverage
Subscribe to our FREE magazine,
FREE email newsletters or both!Latest News
About the Author

DE’s editors contribute news and new product announcements to Digital Engineering.
Press releases may be sent to them via DE-Editors@digitaleng.news.
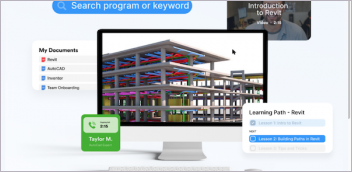
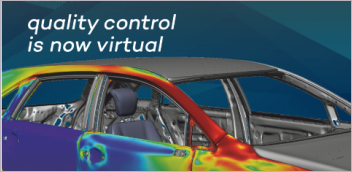
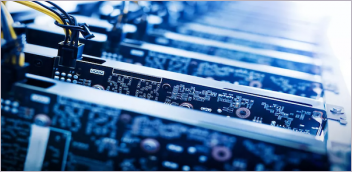
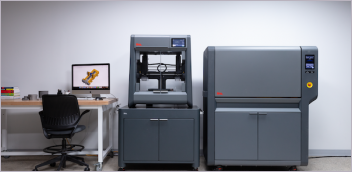