Bobsled Gets a 3D Printed Makeover
CRP USA partners with USA Bobsled/Skeleton team for 3D printed components for the bobsled.

3D printed bobsled parts were manufactured by CRP USA for the USA Bobsled/Skeleton team for the racing season and Olympic games. Image courtesy of CRP USA.
Latest News
December 12, 2023
CRP USA forged a partnership with the USA Bobsled/Skeleton team (USABS). This collaboration involves the supply of 3D printed functional components for racing bobsleds, a venture facilitated by CRP USA's introduction to USABS through a local technical partner specializing in carbon fiber products.
The collaboration has seen extensive meetings between CRP USA's team of experts and the USABS team, resulting in a joint effort to identify the ideal materials for critical components. The 3D printed parts provided by CRP USA include push handles, hand grips and seats, all manufactured using Windform SLS materials. Specifically, two Carbon fiber reinforced composites, Windform SP—which is used for push handles—while hand grips and seats are crafted from Windform XT 2.0.
One advantage of 3D printing highlighted by Marc van den Berg, technology and equipment lead at USABS team, is the time and cost savings achieved. The absence of the need for molds expedites the production process and reduces costs, enabling faster delivery of components, according to CRP USA. The flexibility of 3D printing also allows for the creation of more complex parts.
Despite these advantages, the USABS team faced challenges in complying with regulations related to shapes and dimensions. Stress resistance emerged as a critical factor, especially given the significant forces experienced by bobsleds during races and potential crashes. The selected Windform materials addressed these concerns by providing flexibility and strength, preventing part breakage.
The customization of components, such as push handles, demonstrated the efficiency of 3D printing when combined with the right manufacturing materials.
Nathanael “Nate” Baker, senior project coordinator at CRP USA, emphasized the need for easily producible and customizable push handles tailored to each athlete. Windform SP, with its shock resistance and other valuable properties, was identified as the optimal material for these specific components.
Upon successful 3D printing with Windform and delivery of the push handles, the USABS team conducted some tests, assessing stress resistance and ergonomics. The ability to iterate quickly without the need for expensive molds allowed for optimal design adjustments. The 3D printed bobsled push handles withstood a real race crash, meeting the team’s requirement of remaining intact.
The collaboration reached a significant milestone as the 3D printed parts made their official debut at the IBSF North American Cup (NAC) from November 15-19, 2023. The USABS team achieved outstanding results, securing victories in 2-man bobsleigh, Women’s monobob, 2-woman bobsleigh, and 4-man bobsleigh events, CRP USA reports.
The case study text can be accessed on the Windform website.
Sources: Press materials received from the company and additional information gleaned from the company’s website.
More CRP Coverage
Subscribe to our FREE magazine,
FREE email newsletters or both!Latest News
About the Author

DE’s editors contribute news and new product announcements to Digital Engineering.
Press releases may be sent to them via DE-Editors@digitaleng.news.
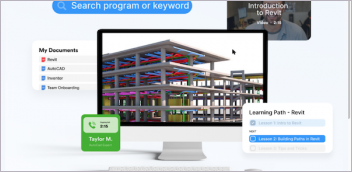
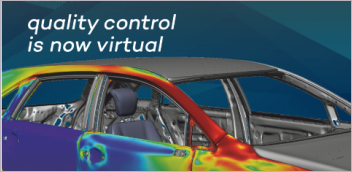
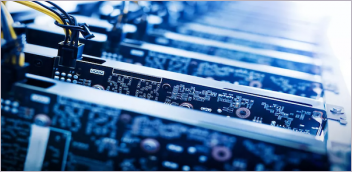
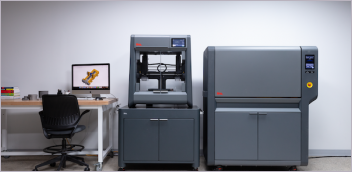