
Pressure distribution around a car body due to a sound source at the exhaust orifice is pictured. Image courtesy of Volvo.
Latest News
January 1, 2015
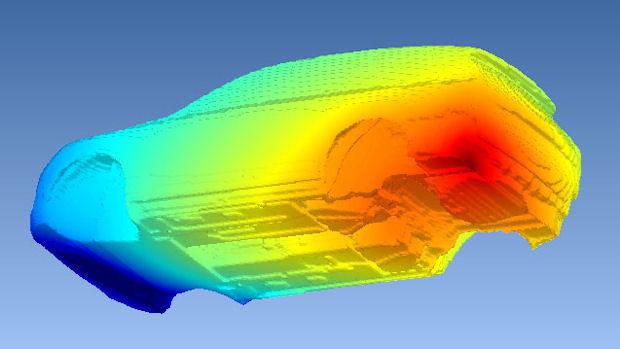
One of the most important customer-facing elements of any new vehicle is NVH (noise, vibration and harshness). NVH directly impacts the customer experience and helps identify the quotient of quality put into the design and construction of a new automobile.
NVH is such an important part of new vehicle design that today’s auto manufacturers invest millions of dollars into engineering solutions to simulate NVH before moving a vehicle into production. Swedish auto manufacturer Volvo Car Corporation is no exception. Volvo Cars has made significant investments into both HPC (high-performance computing) hardware and CAE software to support its engineering teams’ quest to master NVH.
Volvo Cars’ Andrzej Pietrzyk, advanced engineering leader, Body and Vehicle NVH CAE, says his group uses several different products to focus on their core tasks of supporting new product development.
“In NVH CAE, the focus of MSC Software products is on body NVH, so the typical analyses are evaluating the dynamic stiffness, vibration transfer functions, noise transfer functions and acoustic transfer functions,” he says.
Volvo Cars has adopted several modules from MSC, including Nastran, 2013.1 and 2014.0, MSC Actran v14.1, v15.0, MSC Adams, and MSC Marc and other modules. Naturally, running all of those modules takes some serious computing power, explains Pietrzyk.
HPC for NVH
“Currently, we have a set of multi-node servers, typically using state-of-the-art processors, lots of memory and large advanced disk systems,” he says. “We run on 50 nodes, each equipped with double Intel Xeon E5 8-core CPUs, 256GB memory and 5TB fast disk systems.”
The goal at Volvo Cars is to be able to perform simulations as quickly as possible, allowing the engineers to delve deeper into the various vehicle designs to determine how changes impact NVH. With simulation processing time a major concern, Volvo Cars has sought out applications that can leverage HPC technology, leading to ongoing selection of MSC’s platforms and modules.
Pietrzyk says some typical solution sequences used by his group involve MSC Nastran ACMS, a product that can divide workloads across multiple domains using distributed memory parallel processing.
“For those applications, we can cut the solution time by a factor of 4-5 by running on several hosts simultaneously,” he says. “In applications involving the SOL 108 (a select solution sequence in Nastran) procedure, the scaling is linear, meaning that adding more hosts results in the corresponding reduction of the solution time. Running on 16 hosts instead of one leads to the solution time being cut by a factor of 16.”
While that proves to be an impressive gain, Pietrzyk explains that additional performance gains will be realized down the road, thanks to innovations in both HPC systems and CAE software solutions.
The Hardware-Software Gap
Yet, leveraging those additional possibilities remains a challenge. Hardware improvements seem to be outpacing software improvements.
“We are concerned with the growing gap between the development direction of the computing hardware and the algorithms used in the software,” Pietrzyk says. “On the hardware side, the development goes into offering massively parallel solutions, with literary hundreds of cores sharing memory, and unlimited possibilities to extend the number of nodes (distributed memory). On the software side, we do not see the corresponding development toward massively parallel processing. We see bottlenecks in the bandwidth of memory access for systems with many cores and in effective utilization of distributed memory solutions.”
Pietrzyk currently uses 16-core machines, which he says are not being used efficiently, so moving to even higher numbers of cores becomes an issue. Some algorithms do not scale well over DMP (distributed memory parallel), or are limited in the number of DMP hosts that can be used by a single analysis, he says. For many using CAE, a viable alternative may be to use GP-based GPUs (GPGPUs) to speed up computations. However, Pietrzyk currently discounts that alternative for NVH CAE. “The use of GPGPUs for speeding up computations has been considered, but we haven’t seen much effect in our types of simulations yet,” he says.
Nevertheless, Volvo Cars has made some great strides applying HPC and MSC’s products to the NVH problem.
“The primary issue we use MSC products for at NVH CAE is the study of the vibro-acoustic response of the car body,” Pietrzyk says. “The aim is to provide suggestions to the design team on how to resolve the NVH issues. Those issues relate to structure-borne sound transmissions at relatively low frequencies, which could be caused by insufficient stiffness at some attachment points or too high levels of NTFs (noise transfer functions) or VTFs (vibration transfer functions) at some receiver positions.”
Pietrzyk says his team recently started looking at airborne issues and incorporating advanced acoustic models. They are working toward supporting the Audio group with simulations concerning the behavior of the loudspeakers when built in into the flexible body.
“Ultimately, our goal is to enable auralization, or the ability to listen to the sound in a yet non-existing car,” he says. “That requires looking at transfer functions from sources outside of the vehicle to the response points inside, as well as looking at exterior noise, both intentional (like different warning signals, e.g. signal horn, alarm siren) and unwanted, such as the pass-by noise.”
According to Pietrzyk, accomplishing those goals means looking at their traditional MSC Nastran, which recently enriched its acoustics offering, and the newly acquired MSC Actran, which is a dedicated tool for modelling and solving vibro-acoustic problems.
“We are looking for a long-term solution for our needs, and MSC’s products, Nastran, Actran, and Adams form a tool that addresses a broad field of applications within NVH CAE group,” Piertzyk says. “We hope that those pieces of software will be further integrated with each other, thus simplifying their use and enhancing productivity.
“We are always looking at possibilities to extend the range of problems covered by the simulation and to improve the accuracy of simulations,” Pietrzyk adds.
More Info
Subscribe to our FREE magazine,
FREE email newsletters or both!Latest News
About the Author
Frank OhlhorstFrank Ohlhorst is chief analyst and freelance writer at Ohlhorst.net. Send e-mail about this article to DE-Editors@deskeng.com.
Follow DE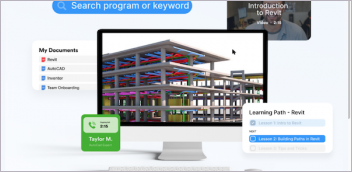
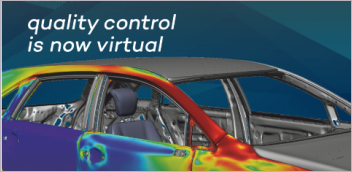
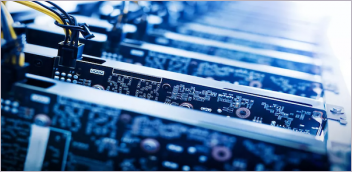
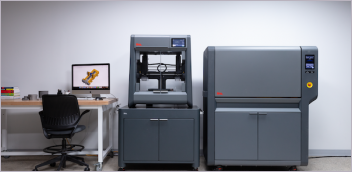