
The Gears PLE Lifecycle Framework provides a common set of PLE concepts and constructs that are intended to enable the integration of tools, assets and processes across each stage of the engineering lifecycle – from requirements and design to implementation, testing, maintenance and evolution.
Latest News
November 2, 2015
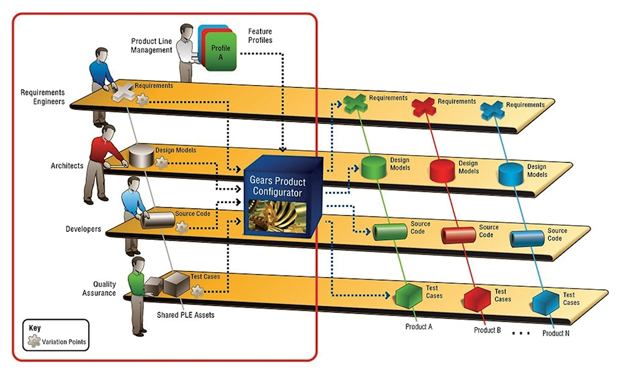
Product line engineering (PLE) could be the difference between success and failure when building most anything. The basic concept behind PLE is creating, automating and managing the processes that allow a related set of products to share engineering assets and effort in order to achieve an efficient means of production. In other words, PLE makes creating things (physical goods, services, software, etc.) easier and more cost effective.
The magic behind PLE comes from identifying and assigning assets to the production process and then managing those assets efficiently, while also identifying where improvements can be found and redundancies eliminated. It’s a concept that sounds like common sense, yet has been difficult to implement beyond the traditional assembly line process of building hard goods.
However, new applications and platforms are changing that and are enabling firms to leverage the concepts of PLE to create almost anything, ranging from products to services to software and infrastructure. “The sophistication of products and systems being deployed throughout the industry requires a commensurate sophistication in the alignment of tools and methods for the traditionally siloed hardware and software engineering,” says Charles Krueger, CEO and founder of BigLever Software. It is that inherent sophistication that drives the need for PLE, and in turn PLE reduces the complexity of building, delivering, maintaining and evolving an entire product line portfolio.
Army Simplifies the Complex
To help implement PLE, BigLever Software is currently partnered with General Dynamics to provide Advanced Product Line Engineering Capabilities for the U.S. Army’s Consolidated Product-line Management (CPM) Next Program. The CPM Next contract, which was awarded earlier this year, allows the General Dynamics-led team to lead the development and management of the Army’s Live Training Transformation (LT2) product line for combat training.
The Army’s adoption of PLE demonstrates how the creation of a complex product line can be transformed to achieve significant improvements in engineering productivity, time to deployment, quality and cost. For the Army, the LT2 product line is one of the most important implementations of PLE, since the end result is the effective combat training of soldiers, while also supporting the rapid deployment of new tactic variations and enhancements to addresses changing missions and threats.
Simply put, by adopting PLE, the Army can better train combat soldiers, regardless of mission and situational awareness changes and achieve goals more efficiently and more reliably. While the Army’s adoption of PLE may be considered an extreme case, it validates that PLE can be applied to critical situations and that production line methodologies are applicable to a wide variety of use cases.
The benefits for the Army were significant. “The Army had a product line concept, but different contractors were implementing their products, creating a divergence from the baseline,” says Roger McNicholas, director of Training Systems and Technology for General Dynamics Mission Systems. “By implementing PLE, we were able converge 22 different products into a single manageable baseline, which brought order to the chaos.”
The goal of the CPM contract was to streamline the process for rapidly adapting training systems and equipment to changing missions and threats. LT2’s PLE approach has delivered significant cost savings to the U.S. Army to date, with more than 200 training ranges worldwide that can scale from individual soldiers to full brigades participating in live force-on-force and force-on-target training.
Naturally, combat training proves to be a critical product for the Army to deliver to its soldiers and using PLE to improve the product comes with other benefits. “Some of the immediate benefits included reducing some 26 million lines of software code to just 5 million lines of code. Also the implementation of PLE expedited product maturity and offered a 300% increase in PDSS (post-deployment software support) efficiency,” says McNicholas.
That said, there was an even more impressive financial benefit the Army realized from deploying PLE. The reuse cost avoidance is $660 million and sustainment cost avoidance is $86 million, so the LT2 total lifecycle cost avoidance is $746 million over 10 years, according to BigLever. That’s a fancy way of saying that the Army potentially saved almost three-quarters of a billion dollars by adopting a production line ideology, backed by the software tools to manage and control the process.
Implementation Strategies
Although PLE can offer significant benefits and savings, it is not a plug-and-play technology. Those looking to adopt PLE will face some hurdles on the path to success. “Implementing PLE is going to take the appropriate software tools, governance and most importantly, a team willing to change,” says McNicholas.
Team culture is a big part of the equation; McNicholas noted that “It is surprising how much time it takes to change the culture.” Some of McNicholas’ other observations include “discovering how much redundancy there is when you peer under the hood of an existing process” and “how collapsing product teams into a factory concept delivers on the promise of reusability of code and processes.”
PLE and Design Engineering
While those realizations further demonstrate the benefits of PLE, the question remains, “how can engineering firms benefit from PLE?” From Krueger’s point of view, the benefits are obvious. “PLE brings with it a single source of feature truth, which provides a holistic view into the feature variations for a product family. That in turn eliminates the need for multiple feature management mechanisms for multiple tools, which facilitates better interoperability across software and mechanical teams, and ultimately improves cross-functional alignment and communication between engineering and business operations,” Krueger says.
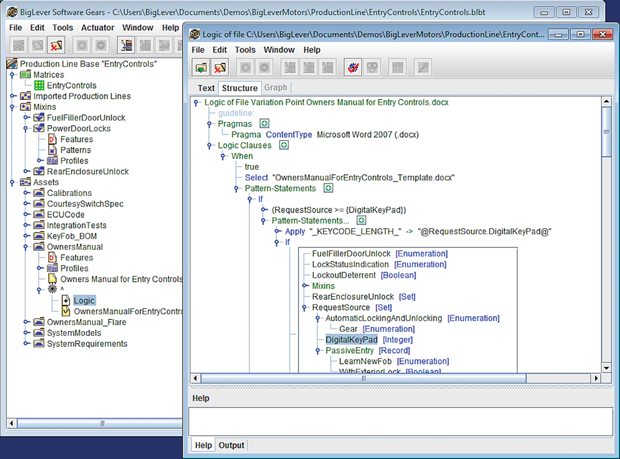
Business speak aside, Krueger is espousing the truth about how PLE transforms production of systems and software (or most anything) from a bill of materials (BOM) based process to a bill-of-features process, which is translated into materials. Those materials can be thought of as anything: mechanical, electrical, wiring, lines of code, calibrations, requirements, designs, test cases, documentation and much more. This can make the bill-of-features ideology appropriate for any production line process.
Ultimately, adopting PLE can help engineering firms to:
• Increase a product line’s scale and scope
• Make more efficient use of highly paid specialists
• Get new products to market faster
• Increase product quality by reducing mistakes
While PLE software is a tool to make the above happen, it is the ideology of the production line-centric approach that makes the process possible. Engineering firms developing large-scale, complex products or delivering engineering services have much to gain from PLE.
Subscribe to our FREE magazine,
FREE email newsletters or both!Latest News
About the Author
Frank OhlhorstFrank Ohlhorst is chief analyst and freelance writer at Ohlhorst.net. Send e-mail about this article to DE-Editors@deskeng.com.
Follow DE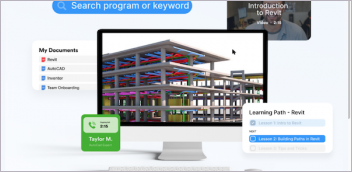
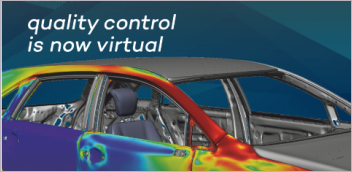
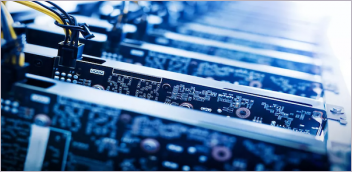
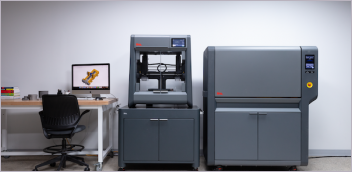