Element Signs Contract With Morf3D
The work for Morf3D will include a full range of materials testing: powder characterization, chemistry, metallurgical, mechanical and fatigue testing.

Inside Element Materials Technology in Huntington Beach, CA. Image courtesy of Element.
Latest News
May 26, 2020
Element Materials Technology (Element) has signed a multi-year contract with an aerospace additive design and manufacturing business, Morf3D, to provide testing centered at Element’s Huntington Beach, CA, laboratory.
The work for Morf3D will include a full range of materials testing: powder characterization, chemistry, metallurgical, mechanical and fatigue testing. The Element team will also perform non-destructive testing at its Rancho Dominguez, CA, laboratory with digital and traditional radiography.
The three-year contract comes on the back of a long partnership between Element and Morf3D in which the business has recognized the benefits of working with Element as testing partner due to location and strength in service standards and technical expertise.
“This long-term partnership with a highly innovative and technically demanding customer like Morf3D is testament to the technical expertise and the high levels of customer service from the Element team in California,” says Rick Sluiters, EVP Aerospace at Element. “Collaborative communication and faster than industry standard delivery puts us ahead of the game in testing for the aerospace supply chain.
“Our extensive testing capacity, preferential pricing and delivery standards offer customers a fully integrated suite of services for technically advanced testing for the additive manufacturing industry.”
“Element’s superior quality, competitive pricing, and high degree of technical competence are all critical elements that create a successful additive manufacturing ecosystem,” says Ivan Madera, CEO at Morf3D. “We are thrilled to extend our relationship and call Element a trusted partner in our expansive value chain.”
Earlier in 2020, Element’s Huntington Beach laboratory announced significant new investment in a full suite of powder characterization technology for the additive design and manufacturing supply chain. New tests include chemical composition analysis; powder sieve analysis; particle size distribution; flow rate; apparent density; tap density; and gas pycnometry.
The laboratory has been providing materials testing and consulting for customers worldwide since 1982. With over 250 highly technical experts and state-of-the-art equipment, the laboratory supports a diverse range of quality requirements, from routine high-volume testing to complex materials analysis and failure investigations.
The laboratory's Nadcap-accredited testing capabilities supply the foundation for quality control and product improvement for many industries along the North American West Coast, including aerospace, military, nuclear and medical manufacturing.
Sources: Press materials received from the company and additional information gleaned from the company’s website.
Subscribe to our FREE magazine,
FREE email newsletters or both!Latest News
About the Author

DE’s editors contribute news and new product announcements to Digital Engineering.
Press releases may be sent to them via DE-Editors@digitaleng.news.
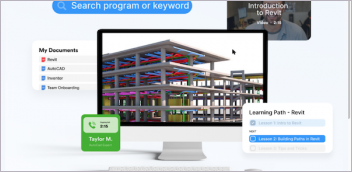
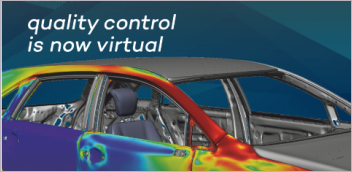
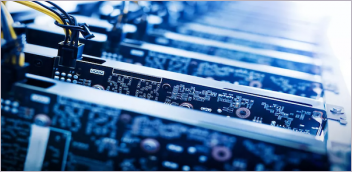
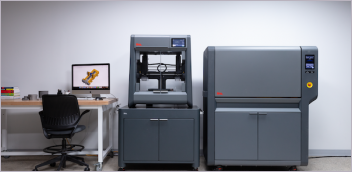